Table of Contents
- Issues with Poor Lamination and Countermeasures
- Handling White Spot Issues in Lamination
- Prevention of Finished Products Roughness
- Addressing Poor Heat Sealing Issues
- Conclusion
- References
Meta Description
Discover solutions to common PE protective film lamination issues, from adhesion challenges to surface imperfections, ensuring top performance and optimal product quality.
body
PE protective films are among the most widely used films thanks to their multipurpose usage in virtually every industry. However, this widespread usage for a plethora of purposes also calls for flexibility and adaptability. PE protective films need to have perfect characteristics depending on the intended use. For example, issues like adhesion strength, thickness of film, degradation, etc, must be dealt with in order to ensure the perfect quality. Let us have a look at the common issues faced during the production of PE films and their solutions.
Issues with Poor Lamination and Countermeasures
Poor lamination and adhesion are among the most common problems in PE films. It can lead to compromising the safety of the product’s surface by exposing it to damaging agents. Here is how the problem of poor lamination can be countered.
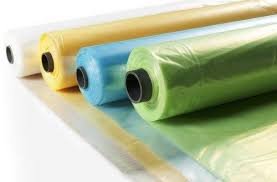
Solutions to Low Surface Tension
PE films naturally have low surface tension causing problems related to adhesion and bonding. Usually, the threshold of 38 dyn/cm is considered to be perfect for lamination. This can be achieved by applying certain surface treatments intended at enhancing surface energy of the PE films. This allows proper bonding and adhesion. Some of the commonly used treatments for this purpose include corona treatment, plasma treatment, flame treatment, and chemical priming.
Analysis of Additive Influence
Additives like slip agents, for example, amines, are used to reduce surface friction and improve handling and processing. However excessive and inappropriate use of additives can compromise the lamination strength of the films. These additives also reduce the bonding capability of films leading to the inefficient ink bonding to the surface of film. High proportion of additives can also weaken the bond between the layers and even cause the layers to be contaminated.
This can be countered by ensuring the minimum possible use of slip agents or combining them with anti-blocking agents to strike a balance between friction reduction and lamination strength. Moreover, using permanent slip agents like silicone can reduce migration to the surface and hence the adhesion is not impacted.
Methods to Avoid Surface Contamination
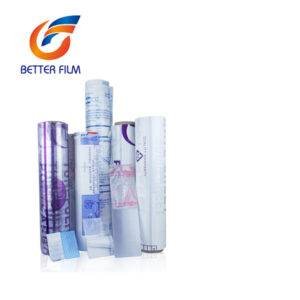
To avoid contamination from the adhesion promoters, optimal amount of adhesives are used instead of using too much of them. Moreover, where possible, going with low volatility adhesives is preferred. Using automated application like gravure and flexographic printing reduces the chances of uneven application, thus avoiding contamination. Using controlled environments helps a lot in reducing the risk of contamination.
Handling White Spot Issues in Lamination
In many cases, white spots appear on PE films, especially in the milky white varieties, compromising the aesthetic appeal. Here are some of the counter measures to avoid white spots on the film.
Importance of Masterbatch Quality
Using high quality titanium dioxide reduces the risk of uneven dispersion of particles in the matrix. It is the uneven dispersion that produces accumulated masses appearing as white spots. Beside using high quality titanium dioxide, the size of particles is also crucial. Using fine, particles that are graded well ensure uniformity reducing the risk of imperfections in appearance.
Solutions to Matt Dot Phenomenon
When the adhesive is applied in inconsistent amount, some areas of the film might appear comparatively dull and matt because the film’s layer do not stick together properly. This problem is countered by ensuring even application of adhesive so that the layers stick together properly throughout the film, not leaving dull or matt spots.
Another solution to this problem is reprinting a layer of white ink on the film. It reduces imperfections in the appearance and masks the matt spots.
Prevention of Finished Products Roughness
Impact of Slip Agent changes
At high temperatures, slip agents in the PE film may undergo degradation, causing loss of functionality and migration to surfaces. This degradation can cause harm to the surface and its texture may appear uneven and rough. To avoid this roughness and degradation of the surface, make sure you have identified the temperature threshold of the slip agent and use controlled temperature settings to avoid surpassing that threshold.
Moreover, choosing stable slip agents like synthetic amides can help increase the threshold as these can tolerate higher curing temperatures without degrading.
Selection of Appropriate Ingredients Based on Use
Inappropriate resin selection can cause defective surfaces. While selecting a resin, melt index and density need to be taken into account. These resins must be capable of withstanding the temperature and processing equipment, and be compatible with additives.
Addressing Poor Heat Sealing Issues
Heat sealing issues are often caused by improperly carried out heat treatment procedures like discharge from corona treatment or due to high slip agent content and the impact of recycled material.
Causes and Countermeasures of Corona Discharge:
When corona discharge is not applied evenly on the surface, the surface energy may vary across the surface resulting in uneven adhesion in heat sealing. Moreover, excessive corona treatment causes the film to become brittle while under treatment results in too low surface energy resulting in inefficient adhesion.
Poor surface tension that does not match the adhesive can lead to poor heat sealing. Hence, it is important to test the surface tension. This can be done through contact angle measurements. Recommended surface tension is ≥38 dynes/cm. This is helpful in avoiding localized discharge and hence poor adhesion.
Problems with High Slip Agent Content
Over-applying the slip agents can result in a negative impact on the clarity of the film due to migration to the surface. It also impacts the bonding capabilities of the film and its heat-sealing consistency.
These issues are countered by selecting appropriate resin grades. For instance, an LDPE and LLDPE blend is a good choice for creating an optimal balance between the quality of the surface and the slip agent’s properties. Moreover, avoid using expired films to avoid problems like degraded surface and migration of additives to the surface leading to defective appearance.
Impact of Recycled Materials on Heat Sealing Performance
Another factor that can contribute to the negative impact on heat sealing performance is the proportion of recycled material. The overuse of recycled material can negatively impact heat sealing. Ensuring a balanced amount can lead to appropriate performance.
Conclusion
PE protective films are indispensable across industries, but their diverse applications demand meticulous attention to production and material selection to ensure optimal performance. Addressing issues like poor lamination, surface contamination, white spots, roughness, and heat sealing problems requires a combination of technical expertise and proactive measures. By implementing appropriate surface treatments, selecting suitable resins and additives, maintaining controlled environments, and ensuring consistent quality checks, manufacturers can significantly enhance the performance and appearance of PE films. Ultimately, aligning production strategies with end-use requirements ensures a reliable, high-quality product that meets diverse customer needs.
References
- https://chidecor.com/product-category/protective-film
- https://www.sciencedirect.com/topics/engineering/corona-discharge-treatment#:~:text=The%20corona%20discharge%20treatment%2C%20one,a%20simple%20process%20to%20perform.
- https://pmc.ncbi.nlm.nih.gov/articles/PMC7040612
- https://chidecor.com/product/pe-protective-film-for-pc-sheet/