Table of Contents
Meta Description
Protect PVC profiles and aluminum materials with protective films to prevent scratches, moisture, and UV damage, ensuring durability, reduced costs, and flawless finishes.
Body
PVC profile and aluminum find their use as preferred construction materials across the globe for almost every type if structure. PVC profile is seen to be used for making doors and window frames. Aluminium is deployed specifically for making facades, roofing, curtain walls, etc. Both are preferred because of their unique and highly desirable properties. For example these are lightweight materials and yet very durable. Both are resistant to corrosion. Moreover, they help reduce energy consumption, making them a desirable material for construction.
However, both aluminum and PVC could do with surface protection as they are used mostly outdoors or at places with high impact. Dust, scratches, and UV rays can damage these materials. Surface protection films help safeguard their integrity and protect them against pollutants, moisture, harsh conditions, extreme temperatures, and UV rays. Protecting them against these agents helps elongate their life span and adds to their aesthetic appeal. Besides, it helps reduce maintenance costs.
Let us have a look at how these surfaces can benefit from protective films and what traits you should look for while selecting a protective film for PVC profiles and aluminum.
Role of Surface Protection Films
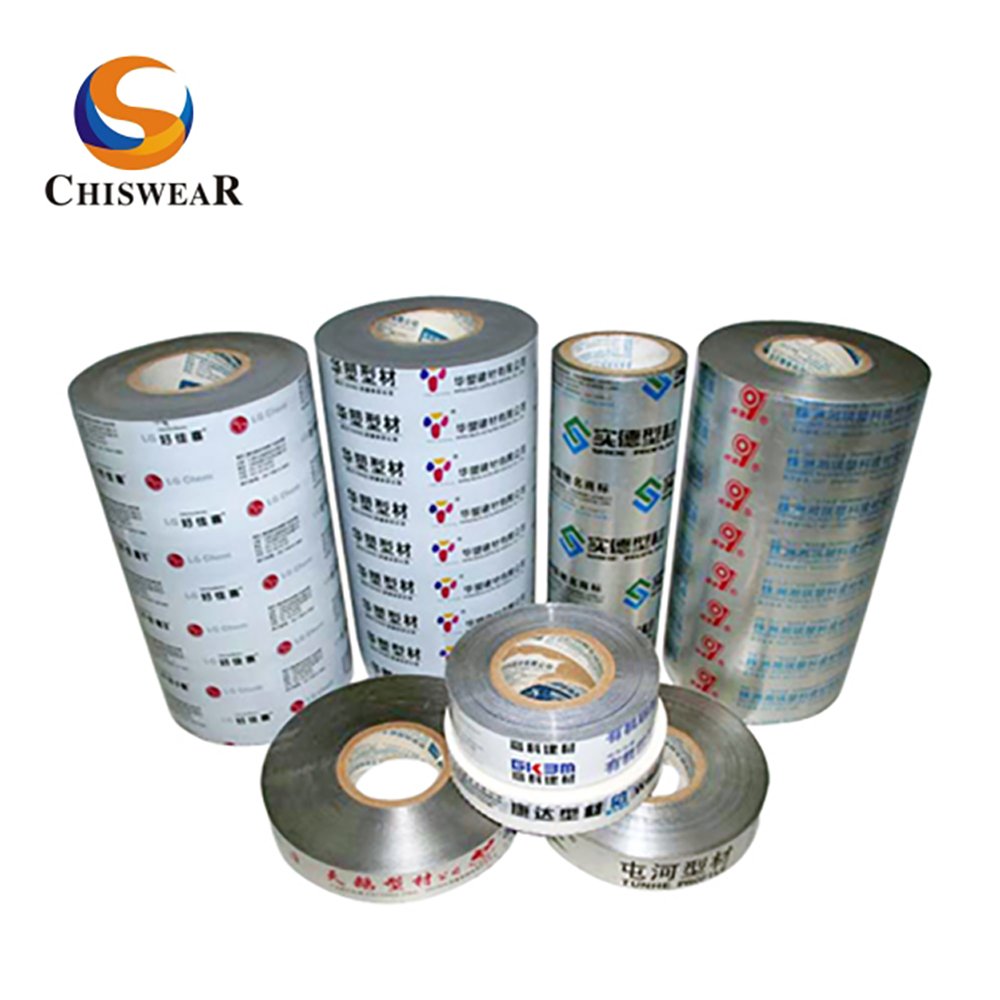
Surface protection films are an ultimate necessity to safeguard PVC profiles and aluminum against various kinds of damages right from the production stage to transportation, storage, and installation. Let’s see how these films add value to the construction material.
Scratch Resistance
In the production phase, various tools, machinery, and debris can cause abrasions on the surface of PVC profiles and aluminum parts. Especially when the aluminum has been anodized, painted, or powder coated, it needs utmost resistance against scuffs and scratches during manufacturing, storage, transportation, installation, and post-installation phases. Protective films help keep them safe from abrasions and keep them in pristine condition throughout.
Protection Against Pollutants
These films keep the pollutants like grease, chemicals, adhesives, dirt, and dust from accumulating on the surface. hence, the surface remains in perfect health and its finish is kept untouched. As all the dirt accumulates only on the protection films. Removing them after installation will reveal the untouched and absolutely clean surface below.
Preventing Corrosion
A quality protection film for PVC profiles and aluminum is meant to withstand humidity, making it difficult for moisture to negatively impact the surface. this added protection helps elongate the material’s life by protecting it against corrosion.
Choosing the Right Protective Film
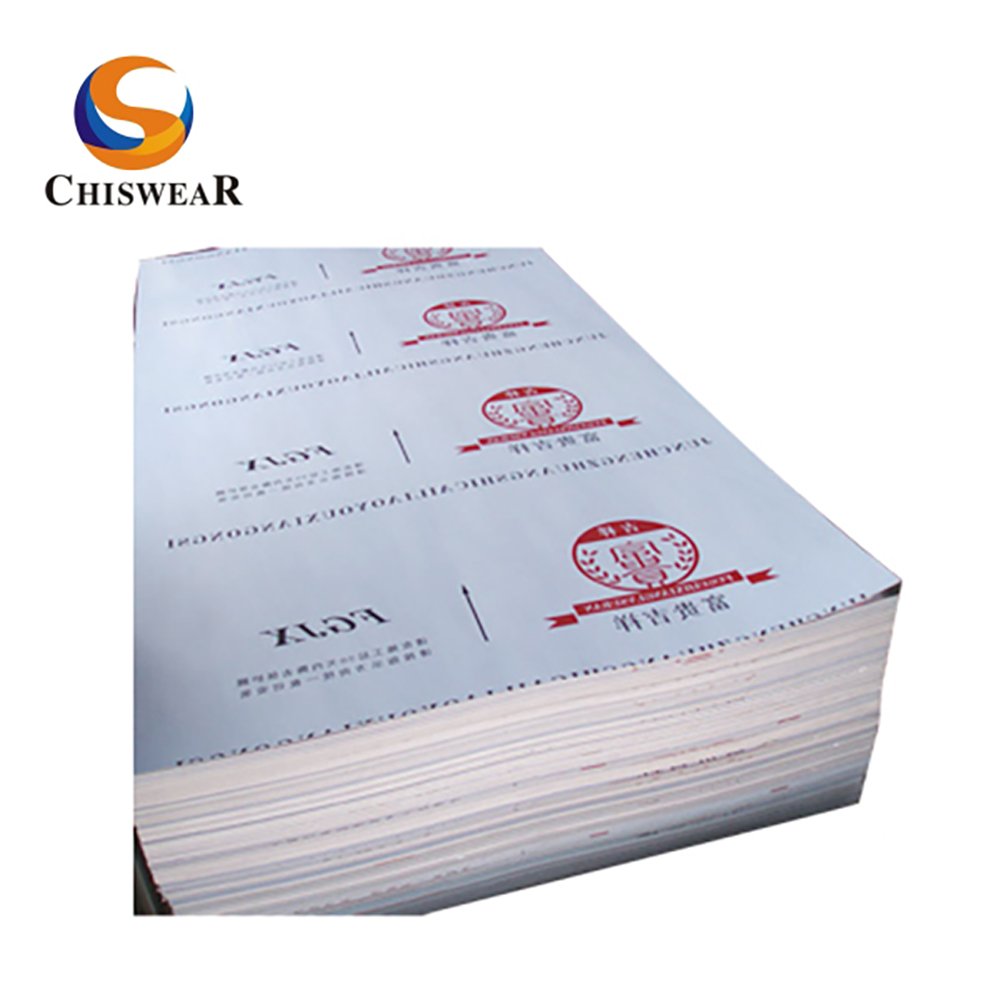
To ensure the utmost protection and get the best out of the protection films, make sure you make the right choice and select the most appropriate films with the characteristics tailored to your specific needs. Let’s have a look at how various factors can impact your choice.
Type of Surface Finish
Not all types of finishes and surfaces can benefit from the same type of protection film. Requirements vary according to the nature of the finish. For example, in the case of PVC profiles, glossy surfaces like window frames require protection films with moderate adhesion. Otherwise, it may leave residue when removed.
Similarly, for aluminium surfaces, the type of protective film would depend upon the type of finish. For anodized and powder-coated aluminium, highly adhesive films might damage the surface. However, for rougher surfaces, films with greater strength should be preferred.
Thickness of Films
If you are looking for medium-level protection to safeguard against dust and pollutants during production, thin films with lower adhesion would do. However, for protection during transportation and long periods of storage, medium thickness of about 60 to 100 microns should be preferred. For protection in outdoor environments and rough settings like construction sites, films with higher thickness would be suitable.
Environmental Factors
For outdoor storage, choose the protection films capable of protecting against UV exposure and dust. Similarly, for surfaces like aluminum which are at a risk of oxidation, protection against moisture is essential.
Case Study
One of our clients in Dubai had a high rise building under construction. He had aluminium façade panels that needed to be stored for at least 6 months before they could be installed in the final stage of construction. These were made with anodized aluminum.
Since these were to be stored on the construction site, they would have been exposed to debris, paint spills, moisture, dust, and other pollutants. To do for these risks, we recommended him to use a protective film with 80-micron thickness and with UV stabilizers added to it. The client was able to protect his façade panels against scratches and abrasions right after the production phase and during transportation, storage, and installation.
Moreover, it also mitigated the risk of oxidation due to moisture as the environment for storage was humid. The added UV stabilizers provided protection against discoloration due to prolonged exposure.
As a result the panels were installed without being damaged in any way. The labor was able to handle them without worrying about scratches during installation and when the film was removed, the surface was in perfectly new condition.
Conclusion
Although PVC profiles and aluminum are amongst the most preferred construction materials in modern buildings, due to their corrosion resistance and being light weight yet durable, they too can easily get damaged. Due to exposure to UV light, moisture, rough handling, and pollutants, aluminum and PVC profiles can undergo surface damage. This is especially true for polished and anodized or powder-coated surfaces that need to be protected even against minor abrasions. protective films help provide them with resistance against such damaging agents and prolong their life-span. These films help resist the damaging agents right from the manufacturing phase to storage, transportation and installation, making sure that the components are installed in a spick and span condition. However, depending upon the nature of the surface to be protected and the environmental settings, make sure you choose the right film to reap the maximum benefits.