Table of Contents
- Impact of Viscosity on the Performance of Protective Films
- Impact of Thickness on the Performance of Protective Film and User Experience
- Practical Examples of How Varying Viscosities and Thickness Can Cause Performance Differences
- How to Select the Most Appropriate Protective Film
- Conclusion
- References
Meta Description
Learn how viscosity and thickness impact the performance of protective films. Discover how to choose the right film for optimal durability, aesthetics, and user experience.
Main Body
Irrespective of which industry you deal in, protective films are needed for every kind of product and at every stage i.e. manufacturing, storing, transportation, and use. Without any surface protecting film, your product will be at a high risk of damage. A high quality protective film elongates your product’s life and makes it more durable by protecting against scratches, decolouration due to exposure to UV light, and corrosion caused by moisture and chemicals. Moreover, these films enhance the overall appearance of the product’s surface.
These are used in virtually every industry. For example, in the automotive industry, a color protective film is used during the production phase to protect the painted surface. Besides, glass protection films are used to protect the windows of the cars and to block UV rays from entering the vehicle. Similarly, protective films are used to safeguard furniture against damage and pollutants. Similarly, screens of electronic devices are protected through thin protective films against scratches during handling. In short, literally every type of product can benefit from these protective films at various stages.
However, selecting the most appropriate protective films demands a thorough research into some of its crucial traits like viscosity and thickness.
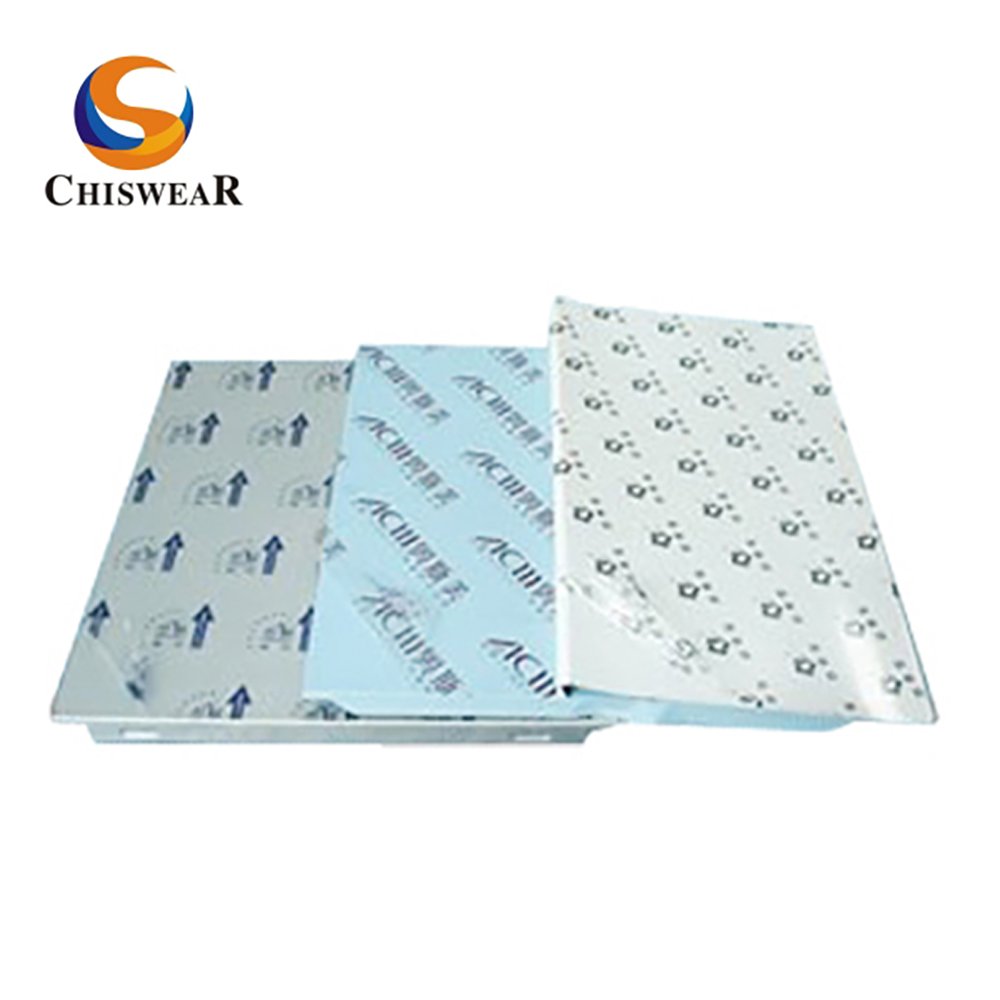
Impact of Viscosity on the Performance of Protective Films
For a basic understanding, viscosity can be termed as the measure of how resistant a liquid is to flow. Those with high viscosity are more flowy. Let us have a look at how viscosity can impact a protective tape’s performance.
· Adhesion
The viscosity of a protective film directly influences its ability to adhere to the substrate. This is because the material used as an adhesive may not evenly apply to such film. Protective films with low viscosity peel off a bit too easily and can not bond properly with the surface. On the other hand, a tape that is too viscous may not come off easily and it may even leave a residue after removal or damage the underlying surface.
· Durability
A protective film with perfect thickness is also important to ensure its durability. Generally, more viscous films are more durable and can provide better resistance against environmental factors. however, these may undermine the overall appearance of the product’s surface.
· Flexibility
The flexibility of a protective film is highly crucial in ensuring that it conforms to the intricate geometries of the product surface. However, it can be negatively impacted if the film’s viscosity is not optimal. A less viscous film may sag. On the other hand, a highly viscous film may not adapt completely to the surface, especially in the case of products with complex surfaces.
Impact of Thickness on the Performance of Protective Film and User Experience
Thickness is another crucial trait of protective films that can significantly impact the performance and satisfaction of the end user. Here is how thickness shapes these aspects:
· Impact Absorption
A thicker film has a greater ability to absorb the physical impact and resist damage to the underlying surface. For example, it absorbs the impact from pressure during rough handling, heat, dents, and scratches. However, a film too thick can undermine the overall look and user experience.
· Durability
Thicker protection films offer greater durability. These do not wear out or tear very easily, hence providing long-lasting protection.
· Aesthetic Appeal
For products where visual appeal has great importance, for example, high-end electronics like mobile phones, the thickness of protective film is very crucial. A thicker film may provide better protection but will compromise the aesthetic appeal of the product. For a sleek appearance, thinner protective film will be preferred in such cases to enhance user experience while still providing reasonable protection.
· Ease of Application
films with higher thickness usually pose application challenges. These are difficult to apply and inefficient application results in bubbles or uneven adhesion. It results in bad user experience and can also impact the protective abilities of the film.
Practical Examples of How Varying Viscosities and Thickness Can Cause Performance Differences
Even minimal changes in viscosity and thickness can lead to a considerable impact on the performance of the film and user experience. let’s try to get a clearer picture with the help of some practical examples:
· Screen Protectors
The difference in thickness of screen protectors, even if it is a few millimeters, can result in a huge difference in user experience as well as the appearance of the device. For example, a protective film for mobile phone screens with a thickness of 0.1 mm does not negatively impact the touch sensitivity and also gives a sleek appearance. However, it does not provide a high degree of protection against impact although it is scratch-resistant.
On the other hand, a film with 0.3 mm thickness provides better protection but can slightly impact the touch sensitivity and make the screen look bulky.
Similarly, a film with low viscosity can be applied more evenly with lesser bubbles. However, it has lesser adhesive power and might come off sooner. On the other hand, a more viscous film bonds better on the screen but can leave residue when removed.
· Stainless Steel Protective Films
A stainless steel protective film with 1-2 mils thickness and low viscosity provides a reasonable degree of protection and does not leave a residue once removed. However, it provides short term protection and should be preferred during manufacturing, transportation, and storage for a limited period. However, a film that is 3-5 mils thick can be used for long-term protection, especially during installation and rough use. But it can leave residue on removal and its application is relatively difficult.
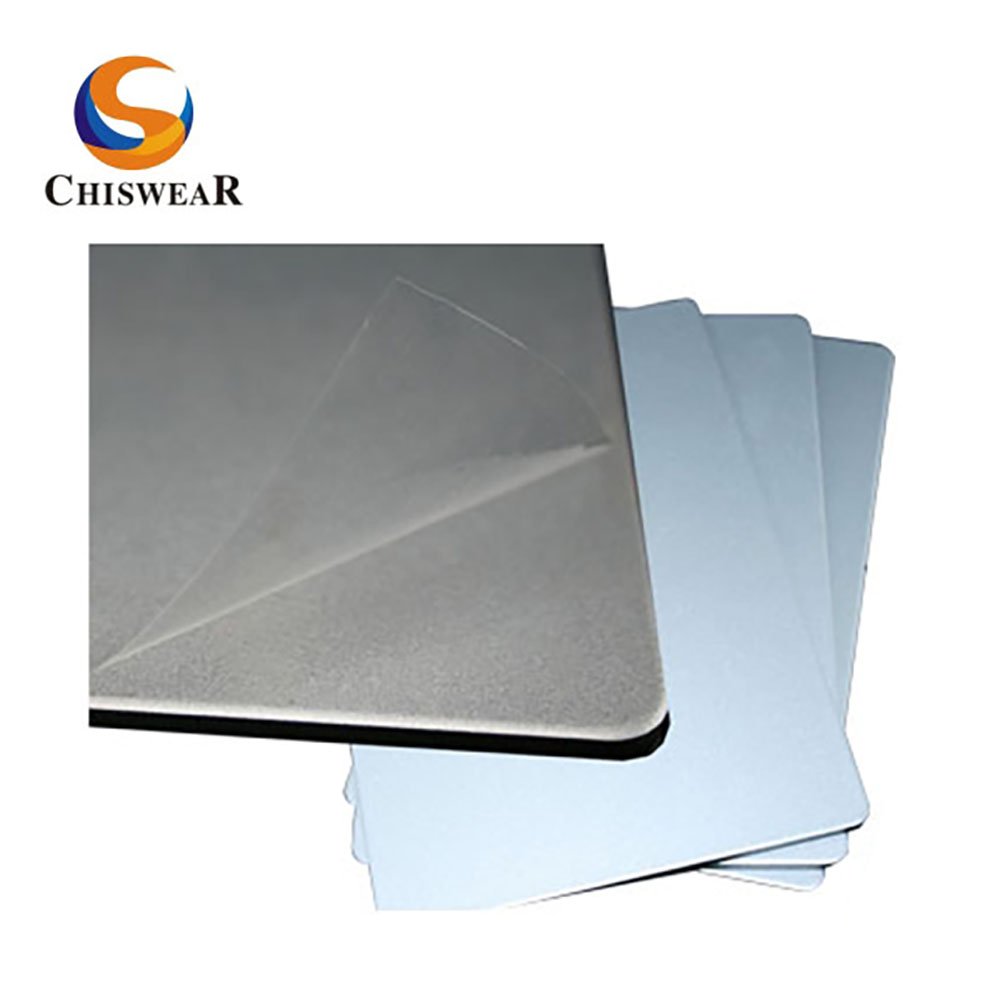
How to Select the Most Appropriate Protective Film
In the end, the best protective film for you would depend on the intended use and time period for which it will be used. It all comes down to your specific needs.
- Make sure you have made a learned choice after considering your particular priorities. Where long-term protection is the goal, you should consider protective films with relatively high viscosity and higher thickness.
- However, when the intended use is for packing, transportation, or limited-time storage, you can save a bit by preferring less viscous and thinner films.
- Moreover, industries where overall look and appeal matters should rely on a balanced combination of thickness and viscosity.
Conclusion
Understanding the roles of viscosity and thickness in protective films is essential for making the right choice to meet your specific requirements. The optimal balance between these two factors can significantly enhance the protective capabilities and user experience of the film. Whether you need robust, long-term protection or temporary coverage, selecting a film with the appropriate viscosity and thickness is crucial. Thicker, more viscous films offer superior durability and impact resistance, while thinner, lower-viscosity options provide easier application and a more subtle appearance. By carefully evaluating the needs of your product and the conditions it will face, you can ensure effective protection without compromising on performance or aesthetics.