Problem 1:
The PE protective film is not firmly attached to the protected product, and it falls off during transportation and use. The reason for this problem is exactly the opposite of the previous problem. The biggest possibility is that the sensitive glue used in the production of the protective film product is not viscous enough. Another possibility is that the pressure of the die press used by the user when applying the mold is not enough, or the surface of the profile is not clean, there is dust or paint, etc., which affects the adhesive effect of the sensitive glue! If this problem occurs, we must target the cause and prescribe the right medicine. Replace the sensitive glue to increase the pressure of the film, or pay attention to the effective cleaning of the surface of the profile when applying the film to avoid such problems.
Problem 2:
After using the protective film for a period of time, the middle performance is good, but the two ends are flared. The main reason for this phenomenon is that the protective film is stretched to a large extent during the pasting process with the protected profile. After pasting, it encounters a high temperature environment and unnecessary shrinkage occurs. This problem often occurs in the products of southern customers. Therefore, the PE protective film should pay attention to the impact of the ambient temperature difference on the product during the production process, and avoid unnecessary surface stretching during the pasting process.
Problem 3:
The most common problem reported by users is the debonding of protective film products. This problem is most reflected in the profile protective film. When the user tears off the protective film from the profile surface after the profile installation is completed, the adhesive on the protective film does not follow the protective film, but remains on the profile product. This is what users are most reluctant to see, because it is very troublesome and requires a special person to scrape the glue off the profile, which is particularly labor-intensive and time-consuming. There are many possibilities for this problem. The biggest possibility is that the pressure glue used in the protective film product does not meet the regulations, that is, it is too sticky, resulting in the external tension of the PE protective film product being greater than the internal stress when it is peeled off, and it remains on the profile. If users encounter this problem, they can use a clean rag dipped in a little alcohol to repeatedly wipe the residual sensitive glue until the sensitive glue is wiped clean. However, it should be noted that you must not wipe too hard when wiping, otherwise it may affect the smoothness of the profile product.
Problem 4:
The protective film product is difficult to peel off. When the profile product is installed and peeled off, the protective film cannot be effectively peeled off. There are two possible reasons for this. One is that the sensitive glue used in the protective film product is not a special sensitive glue for the protective film. If this is the case, the protective film will certainly work very well when pasted, but it will be very difficult to peel off. This is also the most common problem of protective films produced by some illegal protective film product manufacturers. Another possibility is that the material used in the protective film master tape is too soft and cannot withstand the tensile force during peeling, and it breaks when peeling off. This is a very headache for users.
Problem 5:
Although PE protective film products can be effectively peeled off, there are still protective film marks on the surface of the profile. This problem often occurs on some low-grade protective film products. This is because when the protective film is combined with the protected profile, it encounters a suitable environment such as sunlight and moisture, and a chemical reaction occurs. Performance indicators
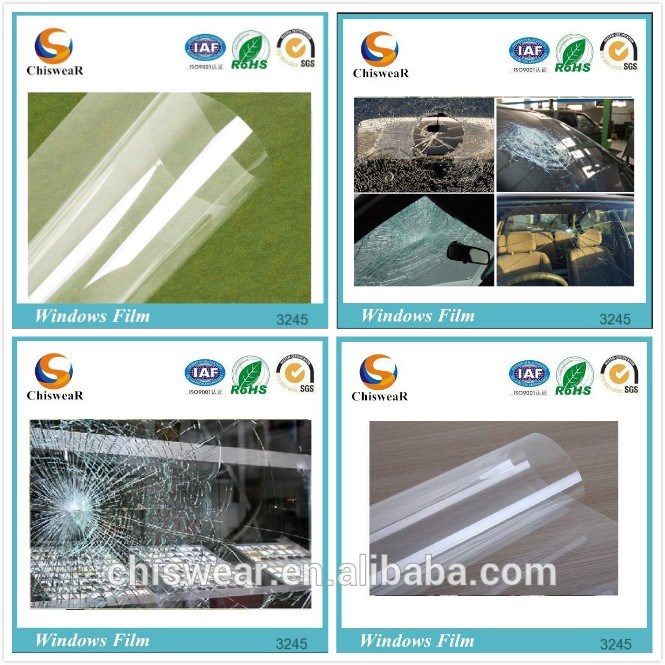
According to the adhesion, they are mainly divided into: ultra-low viscosity protective film, low viscosity protective film, medium-low viscosity protective film, medium viscosity protective film, high viscosity protective film, ultra-high viscosity protective film.
1. Ultra-low viscosity protective film (i.e. slightly low viscosity)
Characteristics: thickness (≥0.03mm±0.003), width (≤1250), length (100-1000), substrate (PE), peel strength (≤20-50g/cm), temperature resistance (60), elongation (>500)
Use: easy to use, easy to stick and tear, no residual glue phenomenon, suitable for organic sheets, instruments, display screens, glass lenses, plastic lenses, etc.
2. Low viscosity protective film
Characteristics: Thickness (≥0.03mm±0.003), width (≤1250), length (100-1000), substrate (PE), peel strength (50-150g/25mm), heat resistance (60), elongation (>500)
Application: Stable adhesion, good adhesion, good re-peeling performance, no residual glue phenomenon, suitable for steel mirror plate, titanium metal, smooth plastic plate, silk screen,
Nameplate, furniture Polaroid board, stainless steel plate, ceramic tile, marble, artificial stone, etc.
3. Medium adhesive protective film
Features: Thickness (≥0.03mm±0.003), width (≤1250), length (100-1000), substrate (PE), peel strength (150-300g/25mm), heat resistance (60), elongation (>500)
Application: Stable adhesion, good adhesion, good re-peeling performance, no residual glue phenomenon, Suitable for fine-grained frosted boards and general hard-to-stick material surface protection, etc.
4. High-viscosity protective film
Characteristics: thickness (≥0.03mm±0.003), width (≤1250), length (100-100), base material (PE), peel strength (300-450g/25mm), heat resistance (60), elongation (>400)
Application: stable adhesion, good adhesion, good re-peeling performance, no residual glue phenomenon, suitable for fine-grained frosted boards, aluminum-plastic boards, hard-to-stick plastic boards, etc.
5. Super high-viscosity protective film
Characteristics: thickness (≥0.03mm±0.003), width (≤1250), length (100-1000), base material (PE), peel strength (450-550g/25mm), heat resistance (60), elongation (>500)
Application: It has extremely high viscosity and uses water-based acrylic as pressure-sensitive adhesive. It is easy to use, easy to stick and tear, and there is no residual glue. It is suitable for difficult-to-stick materials such as rough-grained aluminum plates and carpets.
Usage requirements
1. Suitable viscosity: easy to stick and tear;
2. Stable peeling force: small change over time, that is, the smaller the increase in peeling force, the better;
3. Good weather resistance: under sunlight exposure, the service life is as long as half a year to one year;
4. Long storage period: stored in the warehouse for more than one year, the quality does not change;
5. No pollution, no corrosion: the adhesive is inert and will not react chemically with the surface of the adhered material;
6. Excellent mechanical properties: tensile strength, elongation at break, etc. that meet user requirements.