Profile protective films are made of plastic film or aluminum-plastic composite materials as the base material, coated with low-viscosity pressure-sensitive adhesive on one side, and made into rolls and then cut. Pasted on the surface of the profile, it can effectively prevent the profile surface from being scratched or contaminated during extrusion molding, transportation, window forming, and installation.
Its appearance has brought great convenience to profile production, door and window assembly, and construction units. Since profile protective film is a relatively new product, there is currently no national or industry standard.
There are no unified technical indicators for the inspection and evaluation of product quality. This brings certain difficulties to users when choosing to use protective films. Many profile manufacturers have encountered some problems during use. This article raises these issues for discussion with everyone.
1. Debonding problem
Phenomenon: After the protective film is torn off the surface of the profile, there are traces of glue remaining on the surface of the profile.
The main reason for this phenomenon is the quality problem of the protective film itself. One is that the pressure-sensitive adhesive used in the protective film does not meet the requirements. The technical requirements are not met in terms of formulation and process implementation. The peeling force is greater than the cohesive force; the second is that the corona strength of the substrate used for the protective film does not meet the requirements. The surface tension of the substrate is generally required to be between 3840dyn. If it is too small, the peeling force of the protective film will be greater than the bonding force, causing debonding. If this kind of problem occurs, it is recommended that the profile manufacturer do the following: use a clean rag to dip in an appropriate amount of organic solvents such as ethanol, ethyl ester, toluene, etc. to wipe. This sometimes brings a problem, that is, after wiping with a solvent, the surface finish of the profile will be damaged to a certain extent. The remedy is: you can use a soft dry rag to wipe it several times to restore the finish.
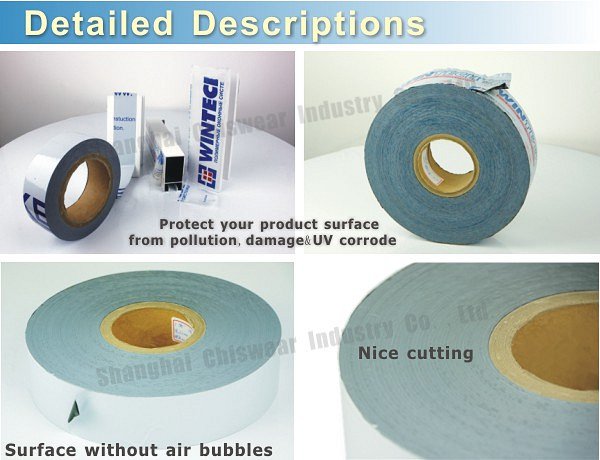
2. The application is not firm
Phenomenon: After the profile is extruded and the film is applied, the film is not firm, and it is easy to peel off during transportation and window forming, and it does not play a protective role. There are several reasons for this phenomenon:
- 1. The surface of the profile is not clean after extrusion and before the film is applied, such as moisture, dust, etc. Improvement method: After the profile comes out of the cooling and shaping mold, try to blow dry the surface moisture, pay attention to the dust in the workshop, keep the traction machine track clean, etc.
- 2. The pressure of the film laminating machine is not enough, or the structure is unreasonable. Solution: Increase the film laminating pressure appropriately; use a special film laminating machine.
- 3. The viscosity of the protective film is not enough.
- 4. The tensile stress of the substrate used for the protective film is too small and it is easy to deform, or the rotating part of the film laminating machine is not flexible, causing the film to be stretched too much and deformed during the application process. After being attached to the surface of the profile, the stress generated by the stretching causes the film to retract. When this retraction force is greater than the peeling force, the film will automatically peel off. For this situation, BOPP, PET or composite protective films with greater tensile force can be used instead; in addition, the rotating part of the film laminating machine should be lubricated frequently to make it rotate flexibly.
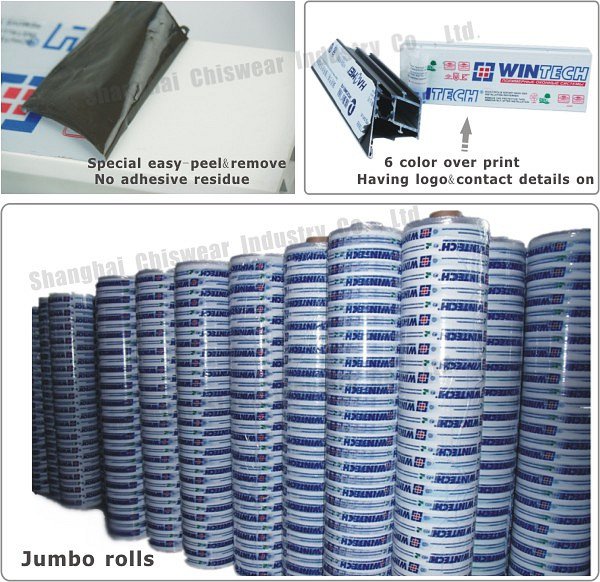
3. Warping at both ends
This phenomenon mostly occurs on profiles with aluminum foil film. It is mainly manifested as the protective film at both ends of the profile warping. The main reason is: during the lamination process of the aluminum foil film, the tension of the BOPP and PET layers is inconsistent, and the tension of the BOPP layer is too large. After the lamination is completed, due to the tension and temperature changes, the BOPP layer shrinks, resulting in warping. It is recommended not to use this film in areas with high ambient temperature and strong wind and sand.
4.the film is difficult to peel off or cannot be peeled off.
Phenomenon: After the doors and windows are installed, it is found that the film cannot be peeled off or is difficult to peel off when peeling off the protective film.
There are two reasons: one is that the quality of the pressure-sensitive adhesive used in the protective film is unqualified. The pressure-sensitive adhesive used in the protective film is a special pressure-sensitive adhesive that can produce appropriate peeling force with the surface of the product, making the protective film easy to apply and easy to peel off. However, many manufacturers currently do not have the production technology of this pressure-sensitive adhesive, but have only made some improvements to the pressure-sensitive adhesive used for ordinary adhesive tapes, or even used it for the production of protective films without any improvements. Of course, the consequences are disastrous. Another point is that after the doors and windows are installed, they are exposed to ultraviolet rays in sunlight for too long outdoors, and the protective film substrate ages, the strength is reduced, and it is easy to tear, which can also cause this phenomenon. Therefore, it is recommended that the construction unit tear off the protective film in time after the house decoration is completed.
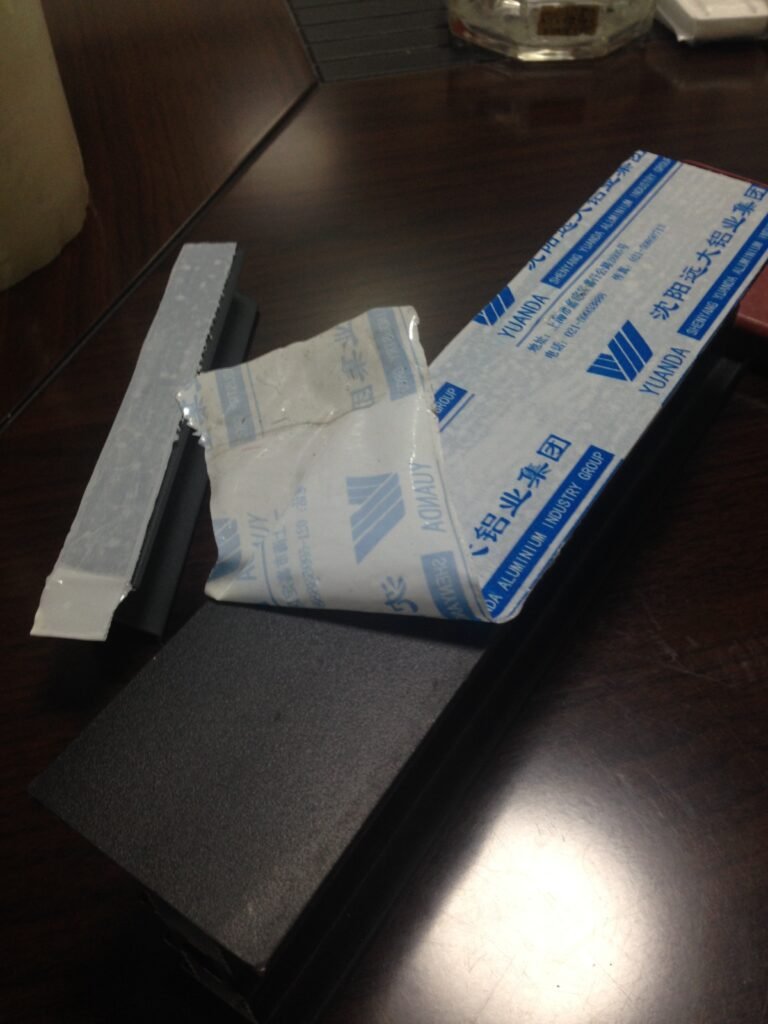
5. There are traces of words on the protective film on the surface of the profile.
Generally, there are two situations: one is that the words on the surface of the profile are black; the other is that the words are the color of the words on the protective film. For the first situation, articles have been published in many publications. Most people believe that this is a chemical change. This chemical reaction must meet certain conditions to occur: moisture, visible light, unstable TiO2. If the above situation occurs, it is recommended to change the type of protective film or use PE two-color film, aluminum foil film, etc. with good light-shielding properties.
For the second situation, it can be definitely considered that the ink of the protective film has migrated. Because the inner composite layer of the protective film is broken down during the corona process. After applying glue and sticking it to the surface of the profile, after a period of time, the ink will migrate to the surface of the profile through the composite layer and glue layer, causing the profile to be printed with words. In order to verify this phenomenon, the author has conducted many tests, selecting profiles and protective films (the same batch of samples that have printed) from different manufacturers for matching tests, and irradiating them under a 250W ultraviolet lamp for 8 hours, but no printing was found. Later analysis showed that the film-sticking conditions during the test were different from those in the production process, and the printing phenomenon reported by users mostly occurred on one or several relatively fixed extrusion equipment, which was not common. The printing phenomenon may be closely related to the profile extrusion process conditions. There is no ideal solution to this problem yet. In this case, it is recommended to use PE two-color film, aluminum foil film, etc.